产品可靠性应该在设计过程得到充分落实,以降低产品故障的概率,为产品的固有可靠性奠定良好的基础。一个只注重功能和性能,而忽视可靠性设计的产品,必然是“先天不足,后患无穷“,往往等到试制、试用后,甚至量产上市后才发现产品存在质量问题,只得再做改进设计,这就使产品研制周期和投入市场的周期延迟,甚至导致大量的产品投诉,严重影响了企业的竞争能力。
可靠性设计的基本任务就是:在满足产品功能和性能(即产品规格需求)的前提条件下,运用可靠性设计的准则和技术方法保障产品能适应在规定时间内,规定环境条件下正常工作。
在产品研制过程中,常用的可靠性设计的技术方法有:元器件选择和控制、降额设计、安全设计、EMC设计、热设计、冗余和容错设计、环境防护设计、人为因素设计、可生产性设计等。这些设计方法应贯穿于系统或产品的总体方案设计、硬件原理设计,PCB设计的完整设计过程中,并不断形成企业的可靠性标准电路库(CBB)、设计准则(checklist)和各种专项设计规范。使其成为企业内部的可靠性设计平台,不断积累和提升公司的研发能力。
q 可靠性设计相关项目
● 产品可靠性设计评审 ● 产品可靠性设计辅导
ü 整机评审(架构、互连、电源、接地、散热、接口) ü 竞品分析
ü 单板评审(BOM、电路原理、PCB设计) ü 产品需求技术规格分析
● 产品可靠性设计整改服务 ü 总体方案(概要)设计
ü 原型设计整改 ü 原理设计
ü DFM/DFA/DFT设计整改 ü PCB设计
ü 样板交付 / 量产交付 ü 设计验证
ü 降成本设计辅导 ü 可靠性预计 / 可靠性分配
● 可靠性技术攻关(烧板、死机、NFF故障不重现问题) ü 板卡/设备/系统 可靠性寿命评估
● 可靠性设计评审流程辅导 ● EMC问题分析、摸底整改、设计整改
● 可靠性设计技术辅导 ● IPD(精简)开发流程及过程技术文档
ü 建立电路公共设计单元(CBB)
ü 建立设计规范(EMC、安规、电源、接地、DFM、接口、防护、PCB工艺...)
ü 建立 DFM/DFA/DFT 设计规范
ü 建立可靠性设计准则 / 评审要素(checklist)
ü FMEA分析及设计
ü 容差分析(WCCA)及仿真
ü 信号完整性SI /电源完整性PI /EMC仿真
ü 热设计(整改) /热仿真
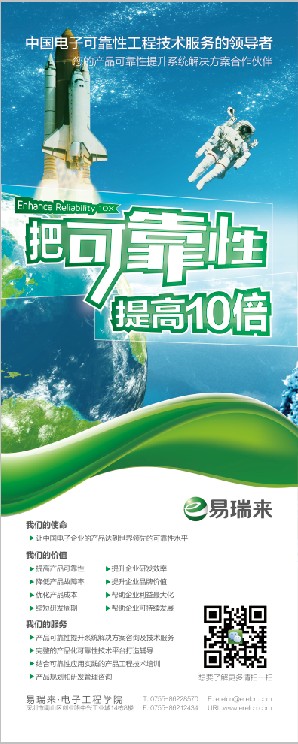