中国现在是制造大国,但还不是制造强国。为什么?
作为消费者,我们都喜欢买美欧日进口产品。为什么?
国内电子厂家经常面临问题:产品问题多导致客户满意度下降;价格只是国外竞争对手的几分之一,利润低,但还是竞争不过,竞争力差。为什么?
重要的原因是:我们的产品质量和可靠性差,国内电子产品和国外领先的差距不是功能性的差距,而是质量和可靠性上的差距。
贵公司是否统计过产品的市场返修率和生产一次通过率?
贵公司是否统计过器件的失效率?
贵公司是否有返修率很高的产品或器件?
贵公司是否统计过单位产品的维修成本?
贵公司是否统计过上述损失成本是多少,占销售收入的比例是多少?
基本现状是:国内很多电子企业的产品生产一次通过率低于90%,市场返修率高于5%,据此推算,这类企业的质量成本将可能达到销售收入的15%。
产品的可靠性是使用的所有器件可靠性的累加。虽然每个器件的失效率仅有几十个PPM以下,但是单板的失效率却可以达到百分之几以上的数据。
某个具体单板上的器件失效不是很平均地表现出来,少数器件的失效率很高,而大多数器件的失效率很少。但是统计更多的产品和单板时会发现,每个器件都存在失效的概率,所有器件的失效率趋于平均。
谁也没有办法准确预测某个单板上哪些器件的失效率高,哪些器件不会失效。要保证产品的可靠性,唯一的方法就是考虑单板上所有器件都存在失效可能,并充分考虑这些器件的主要失效机理,并防止这些失效机理的发生。往往最笨的方法,就是最有效的方法。
一个单板上往往有成百上千个器件,每个器件都有多种主要的失效模式和机理,可靠性工程的目标就是掌握和应用所有器件的主要失效机理以及预防措施。
可靠性是概率事件。一个发展中的企业往往没有足够的能力去控制产品可靠性。能够生存下来往往是“幸运”的结果。 但是,这样的“幸运”不可能伴随企业的一生。随着产品的种类和产量不断扩大,以及时间的推移,不及时提升产品的可靠性,注定会付出惨痛的代价。
国内电子企业的硬件工程师往往是依靠个人的经历来积累一些可靠性知识,不可能全面和深入。 公司层面上大多也没有注重技术积累,可靠性工程的意识、考评机制和方法等都比较缺乏。
以上原因造成了国内企业和工程师的可靠性技术水平停留在初级层面,产品可靠性难以保障。
我们认为:仅靠个人经验和责任心是无法根本提高产品水平的,最主要的是要建立起一套完整的可靠性工程的系统方法,“君子授人以鱼,不如授人以渔”。
可靠性首先是一门专业技术,然后才是一种管理方式。
根据我们的经验,打开电子可靠性工程大门的钥匙是失效分析。
失效分析可以立即准确地解决目前困扰企业最严重的产品问题,效果立竿见影,创造明显的价值。赢得企业领导和大家的认可,并为后续开展可靠性工作赢得必要的支持和投入。
通过失效分析可以积累产品的可靠性设计经验,提高公司研发水平,为后续产品的可靠性打下良好的基础,真正的提高公司的核心竞争力。
三、可靠性工程实施阶段
在产品概念形成之初到推上市场的整个过程中,各个阶段都需要贯彻可靠性工程的理念和实施方法,并积累成为电子可靠性工程平台。电子产品可靠性工程是非常严谨的系统工程,需要高效、明确的流程来保证。
四、电子可靠性工程主要内容
4.1 物料选型认证
物料选型与认证是一项产品工程,是硬件开发活动的重要组成部分。产品一旦选用了某物料,其质量、成本、可采购性基本上60%都已固化,后期的一系列改进、保障策略所达到的效果只能占到40%,物料选型影响重大。如何确定物料的规格,如何识别不同厂家的物料优劣,如何对物料厂家进行认证,如何监控物料厂家的质量波动,这些专项技术,在国际领先公司都有专业的团队来进行研究,并有系统化的流程来保障物料选用,而目前国内厂家普遍比较薄弱,因此从物料选用开始,产品质量就和业界领先公司拉开了差距,可以说是输在了起跑线上。
企业需要建立各类器件的认证规范和选型指导书,提升器件选用过程的效率和质量。通过正确的选型认证来保证构成产品的物料的基本可靠性。
4.2正确合理的设计
常用的可靠性设计方法有如下14种,在产品开发过程中,这些方面都要考虑到,包括借助相应的仿真工具进行分析,以保证设计的产品的可靠性。
① 可靠性预计与FEMA
② 可靠性指标论证、分配与冗余设计
③ 电应力防护设计
④ ESD防护设计
⑤ 降额设计
⑥ 信号完整性分析
⑦ EMC设计
⑧ 热分析和设计
⑨ 容差分析
⑩ 安全设计
⑪ 可生产性设计
⑫ 升额设计
⑬ 环境适应性设计
⑭ 寿命与可维护性设计
国际领先的大公司,对这些设计方法均有专业团队来保障。国内企业如果要提高其可靠性设计水平,应该建立自己的设计准则库(checklist)、标准电路库(CBB)和各种专项设计规范。使其形成公司的可靠性工程平台,不断积累和提升公司研发能力。
4.3 生产工艺严格管控
在加工维护过程中应保证不引入对器件的损伤ESD,产品线的ESD控制水平是多少?
MSD器件的潮湿敏感等级有几级?
造成0603表贴电阻失效的主要原因是什么?
在生产加工过程中,影响可靠性的最主要的因素是ESD、MSD和工艺可靠性,这三方面的控制技术目前发展得较为成熟,也有对应的国际标准,但是国内很多厂家还做得不够完善,如ESD控制不好引发的产品故障问题,往往是在产品到用户手里半年以上会大量爆发。因此怎样控制加工过程,保证对不引入对器件的损伤需要引起重视。在产品维护保养过程中同样要考虑可靠性问题,避免引入对产品的损伤。国内电子企业应该建立或完善内部规范和操作指导书。
4.4 产品测试验证
产品测试分黑盒测试和白盒测试。黑盒测试侧重产品的功能实现,白盒测试则侧重产品的可靠性能。
白盒测试不同于传统的测试技术,传统的测试是求“真”的测试,是针对单板技术规格的确认测试,而白盒测试技术是基于失效机理认知的测试技术,是在求“真”基础上进行证“伪”的测试,能更有效地发现潜在性的问题,更好地提高单板的可靠性。
白盒测试的主要内容包括:
① 信号质量测试:含时钟信号、并行总线、串行总线等等关键信号质量测试。
② 时序测试。
③ 单元电路测试:如电源测试、滤波电路测试、串口电路测试、上下电测试等等。
④ 针对测试发现的问题提出改进建议。
4.5 失效分析
4.5.1 失效分析的产生与发展
可靠性技术的发展源于器件的失效。 研究器件的失效不是简单的定位和维修,而是通过深入分析器件内部的失效特征,找出失效原因,从而为最终解决问题打下坚实的基础。
失效分析是可靠性工程的基础,只有通过失效分析才能从根本上解决失效,降低故障率,积累经验,提高技术水平。
4.5.2 失效分析的目的和意义
传统的器件失效分析是对失效器件进行的分析,从材料、结构、设计、制造工艺和使用等方面,通过物理、化学的分析方法来确定失效模式,分析失效机理,判断失效性质、假设失效原因。
现在的失效分析不仅仅是传统的失效模式和机理的分析,而是根本原因(Root Cause)分析,找到根本原因,提出改进措施,解决问题,更重要的是提出预防措施,在新产品开发中避免类似的问题发生。
4.5.3 典型失效模式
失效模式是器件失效后表现出来的宏观现象和特征,它不需要解剖器件即可获得。主要有:
① 开路
② 短路
③ 功能丧失
④ 功能退化:如漏电流增加,耐压劣化,参数漂移
⑤ 重测合格
⑥ 结构不良
4.5.4 典型失效机理
失效机理是指由于物理、化学、机械、电、人等原因引起产品失效的机理。该定义中的产品是从大的系统到器件、部件、材料等的总称。
如果针对半导体器件的情况,失效机理是导致器件发生失效的物理、化学变化过程,如介质击穿、金铝合金引起键合点抬起、钠离子沾污导致的PN结劣化、闩锁效应引起的烧毁等。根据失效机理,可以判断导致器件失效的根本原因,进而提出相应改进措施。典型失效机理包括:
① 电应力
√雷击浪涌
√ESD
√电源上下电
√带电插拔
√器件闩锁
√过压
√过流
√冲突
② 热应力
③ 机械应力
④ 环境应力
⑤ 寿命应力
⑥ 来料缺陷
4.5.5器件失效分析流程
4.5.5.1 解剖前的过程
解剖前的过程通常可能包括
l 失效情况调查,总结失效数据
l 测试(功能、I-V曲线测试)
l 模拟实验
l 外观镜检
l X-RAY检测
l 超声扫描
l 失效模式分类
4.5.5.2 解剖
解剖(Decapsulation)是利用物理和化学方法对器件解封,其目的是为了对元器件内部进行仔细检查和测试。解剖时应根据封装特点制定出开封方案,避免损伤器件内部的结构、破坏失效部位。
4.5.5.3 解剖后分析过程
器件失效分析思路有两个主要过程:正向和逆向分析。
l 逆向分析,即从器件的失效模式和机理中推测器件的主要失效原因。
l 正向分析,即从检视器件应用是否正确的角度分析。
失效重现是判断失效分析结论是否正确的重要依据,但不是充分依据。因此需要从多个角度验证,避免出现错误结论。
4.5.5.4 编写失效分析报告
根据失效分析获得的各种数据,可以证实失效机理,找出失效原因,制定防止失效再次发生的措施,并写成失效分析报告,使成果共享。
五、易瑞来的产品可靠性工程
5.1可靠性工程五大技术平台
国内电子企业如果要自行建立上述可靠性的五大技术平台,需要投入的可靠性技术专家至少20人以上,花费时间在5年以上,可靠性设备投入在1000万元以上,累计投入在1亿元以上。国内企业往往无法承受如此巨大的投入,而且国内可靠性技术专家非常匮乏,无人可用。但如果没有这些5 大技术平台的支撑,设计制造出的产品有很大的质量风险。
针对这种情况,易瑞来建立了物料选型认证、可靠性设计、产品测试、生产可靠性和失效分析五大平台,对企业提供专项技术咨询和外包服务支持。易瑞来科技相当于国内电子企业虚拟的物料认证部、设计评审部、硬件测试部、生产技术管理部和器件失效分析部。电子产品企业通过和易瑞来建立战略协作关系,只需要较少的投入,即可成为易瑞来的合作伙伴,得到持续的可靠性技术服务,从而设计制造出稳定可靠的产品。
(1)物料选型与认证:
一方面针对产品使用的物料进行评审,指导进行物料选型,辅导选择性价比相对最优的适用物料。物料选型可扩展至涵盖公司全部产品的物料,建立起统一的物料优选库。另一方面辅导对关键物料进行认证,包括部分物料的DPA分析,作为选择物料供应厂家的依据和推动供应商改进的依据。项目期间,易瑞来顾问辅导建立物料选型流程、物料规格书和物料技术认证等文件,为企业培养数名掌握物料技术认证能力的员工。
(2)可靠性设计评审及辅导:
从①器件选型、②器件应用、③安规设计、④信号完整性、⑤EMC设计、⑥可生产性设计、⑦热设计、⑧电源可靠性、⑨环境适应性设计等9个维度对整机方案及单板电路进行可靠性设计评审,提出设计改进建议。通过可靠性设计评审报告的讲解和技术交流,提升研发人员的可靠性设计能力,并积累经验。亦可在项目开发之初或整改过程中,就对用户产品从总体方案到设计实施的整个过程进行辅导,实现快速研发,加快产品上市。
(3)硬件单元白盒测试:
对产品中的重点单板,进行硬件单元测试,完成测试报告并提出改进建议,以发现和改进产品在样机阶段潜在的问题,提高产品的稳定性。通过单元测试项目的实施,提升研发人员的测试能力。
(4)生产可靠性改进辅导:
根据硬件电路的生产特点,依据失效分析机理,对产品的生产厂或代加工厂进行ESD、MSD、焊接工艺的审查,发现改进点,并完成《工厂加工技术要求》,以之作为对(代)工厂的要求和审查依据。通过生产项目的实施,尤其是在跟线过程中通过易瑞来顾问的辅导进行生产实际问题的解决,同时可以提升用户对生产工艺过程的管控能力。
(5)失效分析:
针对产品在试产、量产及客户端使用出现的问题,辅导进行数据分析,失效机理分析及原因分类,并针对问题提出改进解决方案。通过双方配合来进行失效分析,提升研发人员对器件失效分析的能力,为后续独立开展失效分析工作打下基础。并且通过失效分析确定需要重点认证的关键物料。
5.3可靠性工程为用户创造价值
基于易瑞来可靠性工程的五大技术平台不仅能大大提升产品的可靠性品质,降低返修率,赢得市场口碑,而且还可以通过物料、设计及生产工艺各方面的管控和提升不断优化产品成本,提升产品的市场竞争力。同时也可以缩短产品从研发到上市的周期,获得市场先机。
举例而言,如果某产品的年产值为1亿元,年返修率为5%,直接损失最低500万元。据经验,失效率排在前3位的器件一般占该单板总失效率的80%以上,找出这3个器件的失效原因,进行整改,则该产品返修率可以在很短时间内降低到1%以下,带来的直接收益为400万元。通过物料优选、产品设计方案的优化在原有设计基础上使硬件电路部分的综合成本也能下降5%甚至以上,则由此带来的直接利润又增加500万元。通过生产工艺的管控,简化工艺环节,提高产品的一次直通率,同样能为企业节省1-2%左右的成本。而总体改进带来的每年的间接收益可能远超过1000万元以上。由此不仅提升了产品价值,也为企业赢得了更丰厚的利润和良好的市场口碑。
在可靠性工程实施的过程中,也使用户的研发团队拓宽视野,逐步建立起可靠性系统工程的理念,并能在实践中借鉴、理解和运用可靠性工程的先进技术和实用方法,从而为企业研发体系产品化能力的提升以及公司的持续发展奠定了良好的基础。

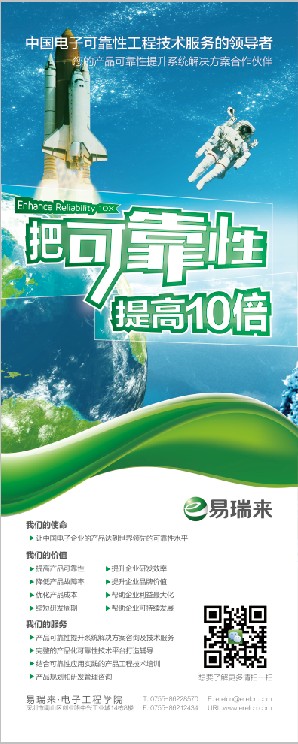